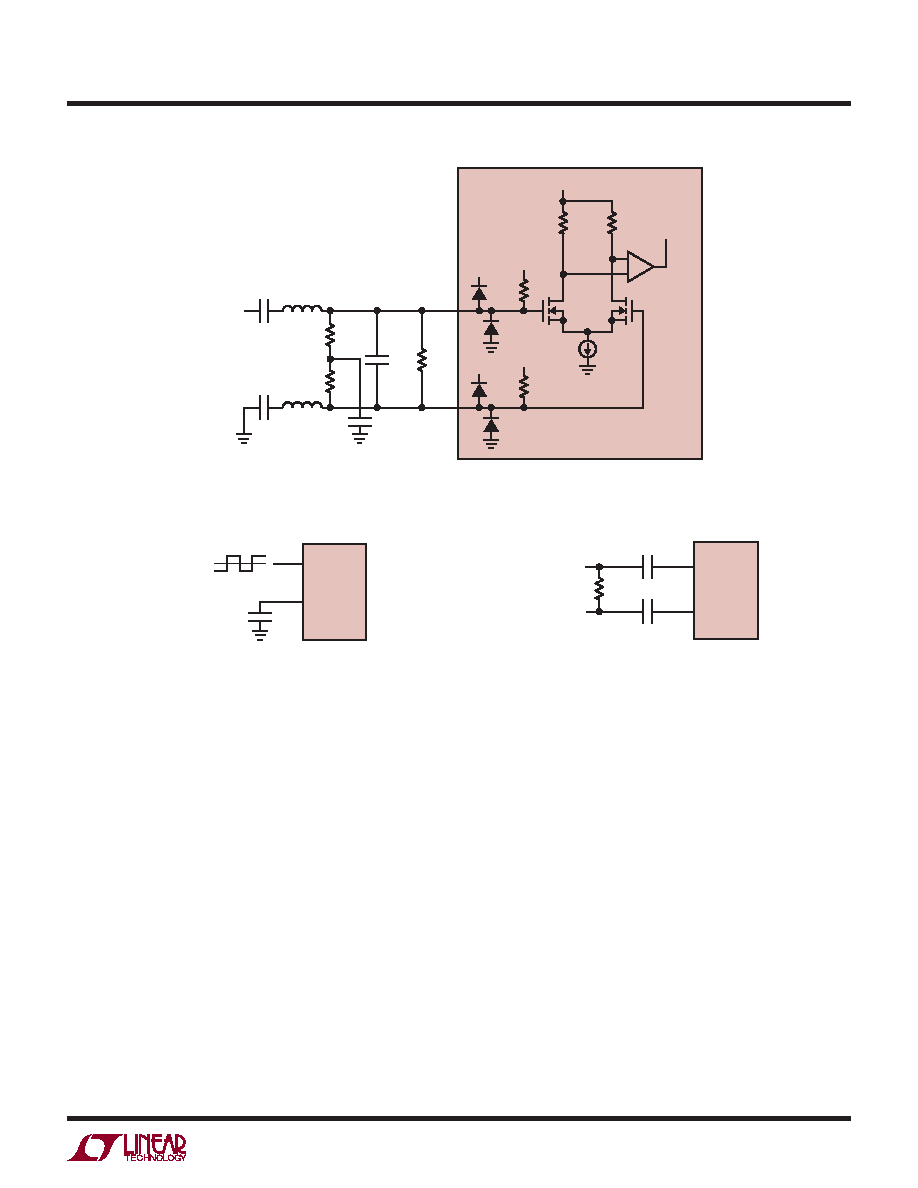
LTC2242-10
19
224210fd
applicaTions inForMaTion
Maximum and Minimum Encode Rates
ThemaximumencoderatefortheLTC2242-10is250Msps.
For the ADC to operate properly, the encode signal should
have a 50% (±5%) duty cycle. Each half cycle must have
at least 1.9ns for the ADC internal circuitry to have enough
settling time for proper operation. Achieving a precise
50% duty cycle is easy with differential sinusoidal drive
using a transformer or using symmetric differential logic
such as PECL or LVDS.
An optional clock duty cycle stabilizer circuit can be used if
the input clock has a non 50% duty cycle. This circuit uses
the rising edge of the ENC+ pin to sample the analog input.
The falling edge of ENC+ is ignored and the internal falling
edge is generated by a phase-locked loop. The input clock
duty cycle can vary from 40% to 60% and the clock duty
cycle stabilizer will maintain a constant 50% internal duty
cycle. If the clock is turned off for a long period of time,
the duty cycle stabilizer circuit will require one hundred
clock cycles for the PLL to lock onto the input clock. To
use the clock duty cycle stabilizer, the MODE pin should be
connected to 1/3VDD or 2/3VDD using external resistors.
ThelowerlimitoftheLTC2242-10samplerateisdetermined
by droop of the sample-and-hold circuits. The pipelined
architecture of this ADC relies on storing analog signals on
small valued capacitors. Junction leakage will discharge
thecapacitors.Thespecifiedminimumoperatingfrequency
for the LTC2242-10 is 1Msps.
DIGITAL OUTPUTS
Table 1 shows the relationship between the analog input
voltage, the digital data bits, and the overflow bit.
Figure 11. Transformer Driven ENC+/ENC–
Figure 12a. Single-Ended ENC Drive,
Not Recommended for Low Jitter
Figure 12b. ENC Drive Using LVDS
VDD
LTC2242-10
224210 F11
VDD
ENC–
ENC+
1.5V BIAS
0.1μF
T1
MA/COM
ETC1-1-13
CLOCK
INPUT
100Ω
8.2pF
0.1μF
50Ω
50Ω
4.8k
TO INTERNAL
ADC CIRCUITS
224210 F12a
ENC–
1.5V
VTHRESHOLD = 1.5V
ENC+
0.1μF
LTC2242-10
224210 F12b
ENC–
ENC+
LVDS
CLOCK
100Ω
0.1μF
LTC2242-10
0.1μF